WRITING & PRINTING PAPER
In general following steps are involved in paper making process
Raw Material Preparation
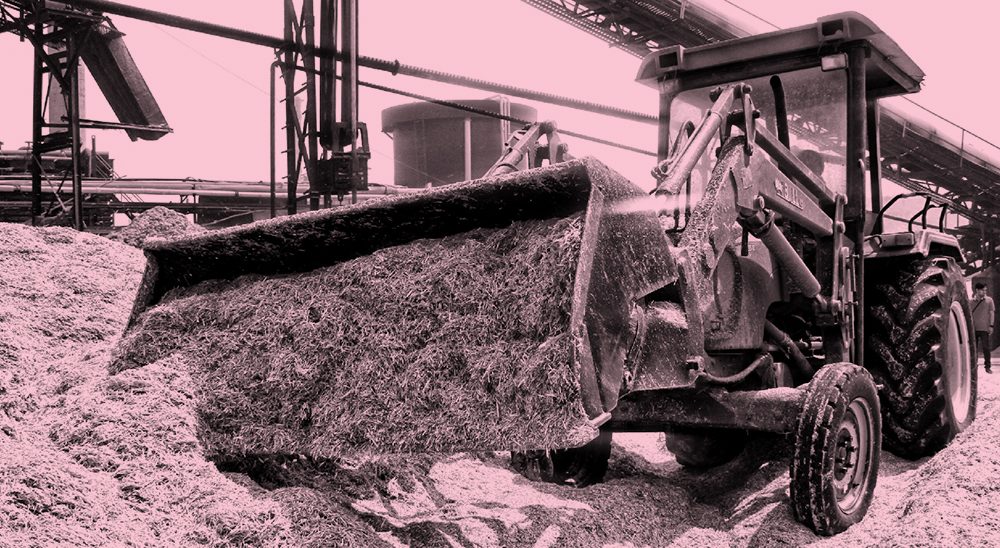
Agricultural residue like wheat straw, bagasse & sarkanda are basic raw material being used for paper making. First of all dry depithing is being done through duster drum & depithers to remove dust, sand and fines followed by wet washing to further remove the attached soil and sand etc in twin turbo washers and aqua separator.
Cooking
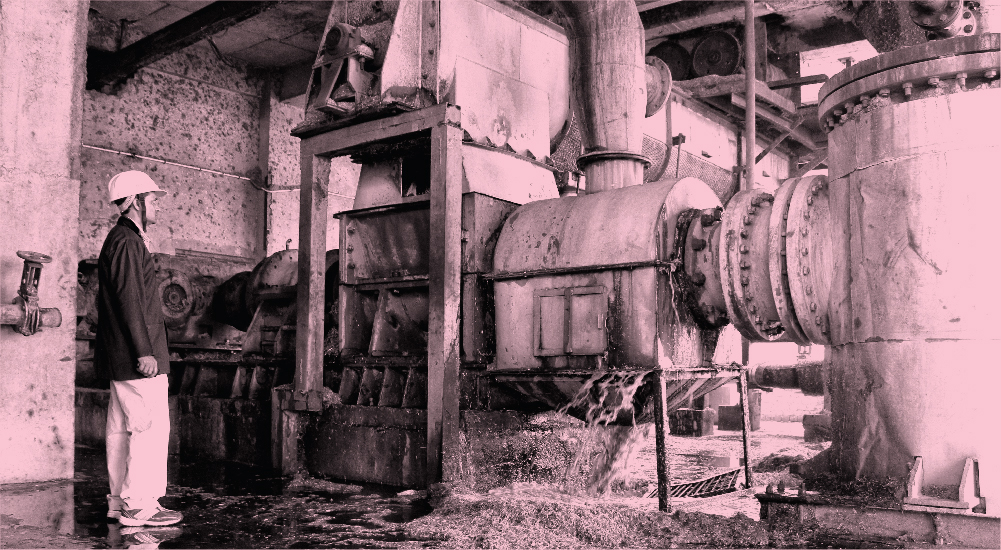
Depithed & washed raw material is cooked in Continuous digester along with White liquor & steam at desired temperature and pressure to get cooked pulp. Continuous cooking process has its own advantages of uniform quality, efficient utilization of chemicals and steam.
Washing & Screening
Cooked pulp is washed through four stage counter current Brown stock washing with hot water (coming from Soda Recovery plant evaporator) followed by three stage pressure screening & three stage centri cleaning to remove uncooked material like knotts &
sand etc.
Black liquor recovered from washing is send to Soda Recovery
plant for further recycling and recovery of chemicals & steam.

Bleaching
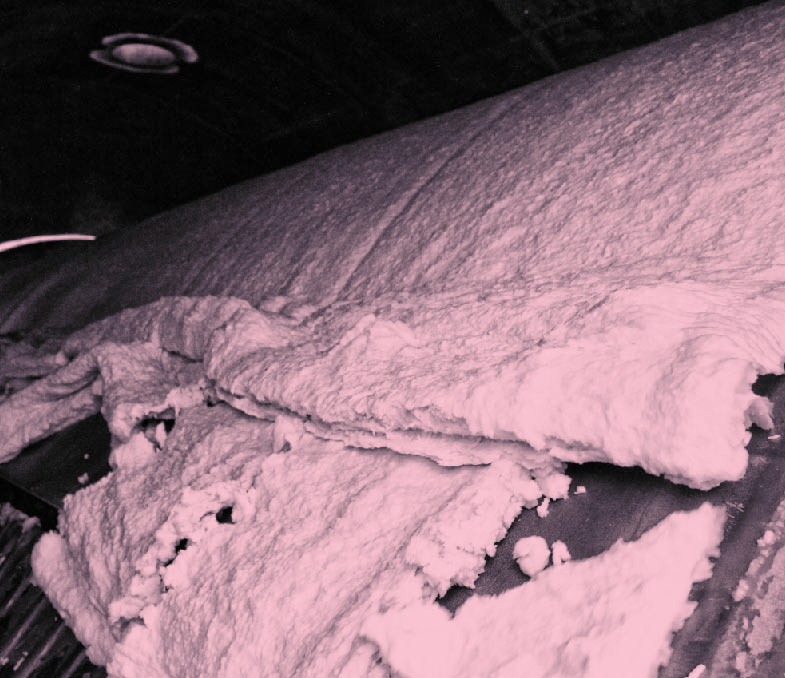
Washed & cleaned pulp is processed in three stage bleaching having sequence DO Ep D1 with proper mixing of chemicals and steam to get desired quality of bleached pulp of brightness 83 – 84 deg ISO.
Chlorine di oxide bleaching gives better brightness, more strength, no color reversion after paper making.
In Ruchira, we have ClO2 plant of Hpa process supplied by M/s Protech Chennai.
In pulp mill water consumption is 10-12 m3/MT of Bleached pulp
by recycling of Machine back water and pulp mill water.
We are using liquid oxygen in pulp mill & ETP to maintain the quality of pulp and ETP dissolved oxygen of final effluent discharge.
Quality Control
Ruchira is having quality control department to check all the incoming raw materials, chemicals, pulp & Paper testing with latest testing equipments.
Chemical Recovery Plant
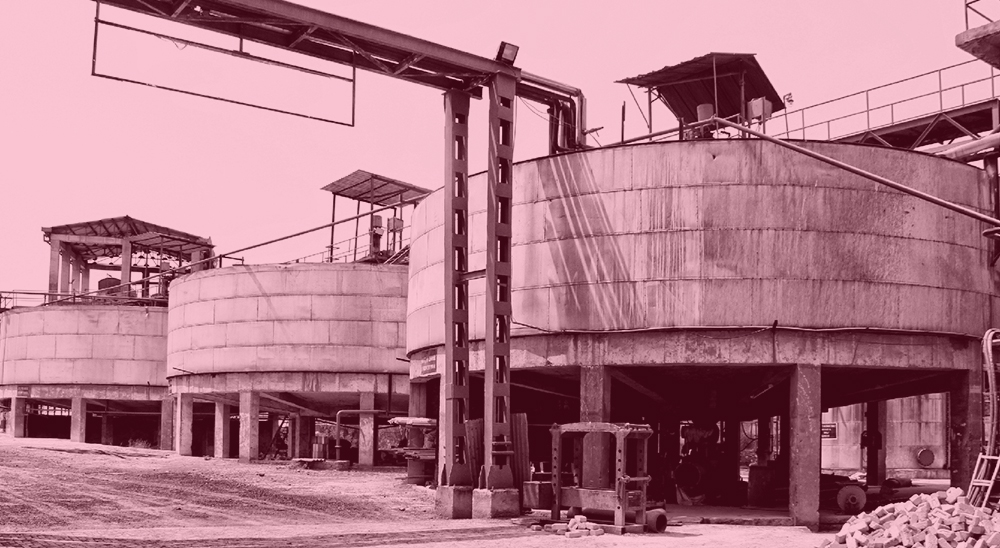
It is equipped with Conventional Recovery system with 2.5 MW turbine running independently on Recovery boiler steam.
Weak Black liquor from pulp mill having concentration 10-11 % fed
to multiple effect parallel flow falling film evaporators with steam
to get 48 – 50 % BLDS with steam economy 6.5 T/T.
This Semi conc. Liquor is taken to direct contact cascade for further conc. before burning in Single drum Recovery Boiler. Carryover dust is collected in ESP & recycled in the process.
Molten smelt dissolved in weak wash form causticizing plant is taken for conversion of sodium carbonate to sodium hydroxide by using high quality quick lime. Thus White liquor is formed and send back to pulp mill for cooking. The Total Alkali recovering is upto 94%.
Stock Preparation
Here various chemicals like AKD, Starch, OBA, Fillers, retention aid, drainage aid, dyes etc mixed in pulp for better strength and shade
of final paper in different ratio in different grades.
We add 3 – 5 % imported soft wood also for better strength
properties of paper.
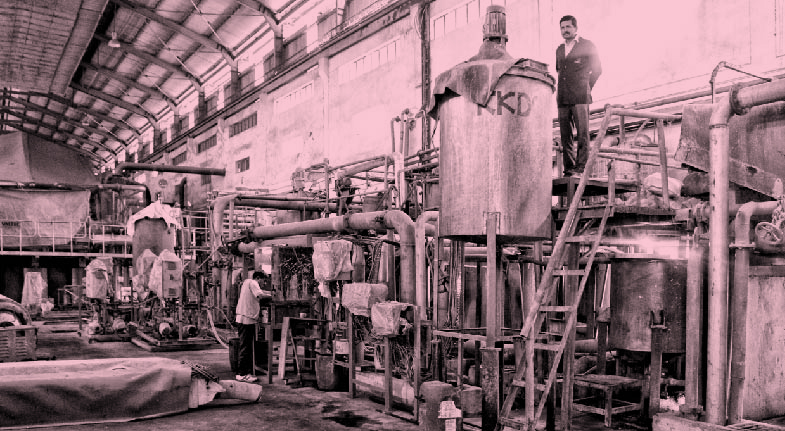
Paper Machine
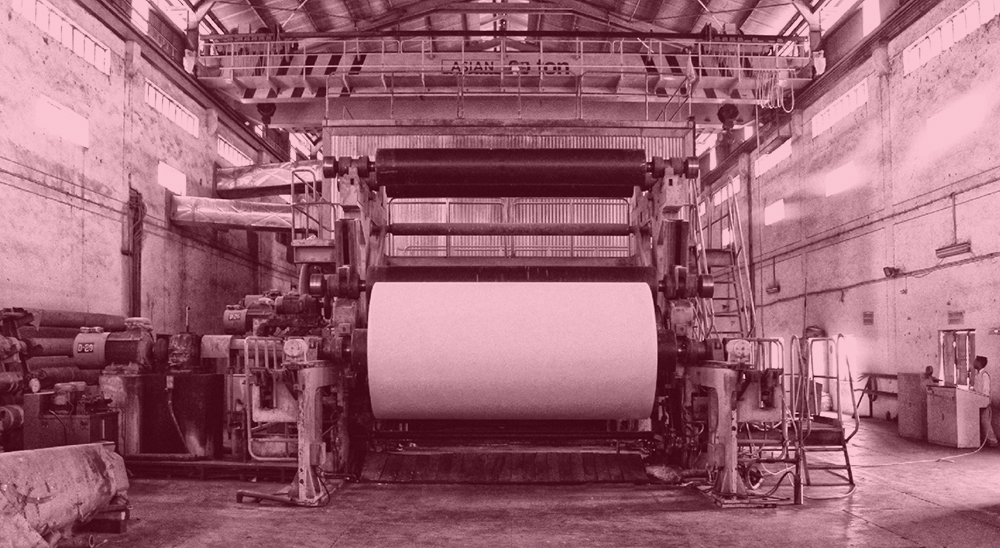
Our paper machine is state of the art having most advanced technology and equipped with latest parts. In paper machine, dilution head box is installed for more accurate CD profile control-interface with on line QCS (Quality control system-scanner) to maintain 2 sigma basis weight, caliper & moisture control.
Our GSM range at paper machine is 49 to 170. Machine is equipped with Top former for two side de watering, better filler distribution on both sides of paper and to minimize two sidedness. Ceramic dewatering elements are from Europe for top & Bottom wire.
Bi Nip Press with separate 3 rd press having Stone roll on both sides of paper for better & minimal Two sidedness Closed Hood Equipped with Proper Air handling system with Humidity / Zero level control through PLC system.
Hard Nip Calender with Thermoroll (Oil circulation & Temperature Control) & Crown controlled (Cc roll) for uniform Smoothness and Caliper across the width of the paper ON Line Scanner for MD / CD Basis weight , MD Moisture & MD Ash control
Equipment Reliability
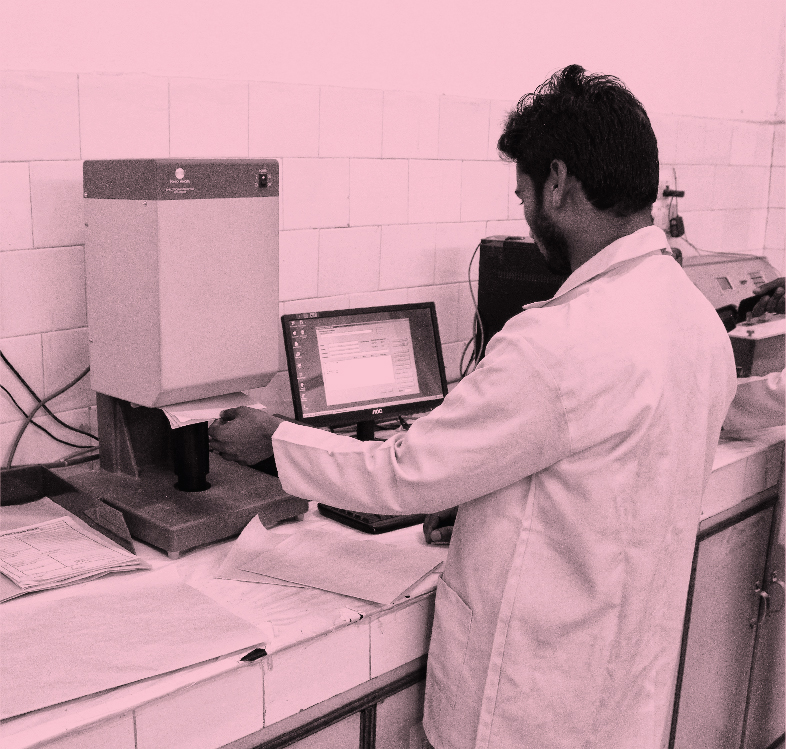
To ensure Equipment reliability, vibration measurement and analysis of each and every equipment is done at site with dynamic balancing, laser alignment, Oil analysis, IR thermography, ultrasonic testing of compressed air leakage detection, RCFA on bearing failure.
For Energy conservation, complete plant lighting is changed with latest LED tubes & bulbs.